What Is the Difference Between Locking and Non-Locking Wheels?
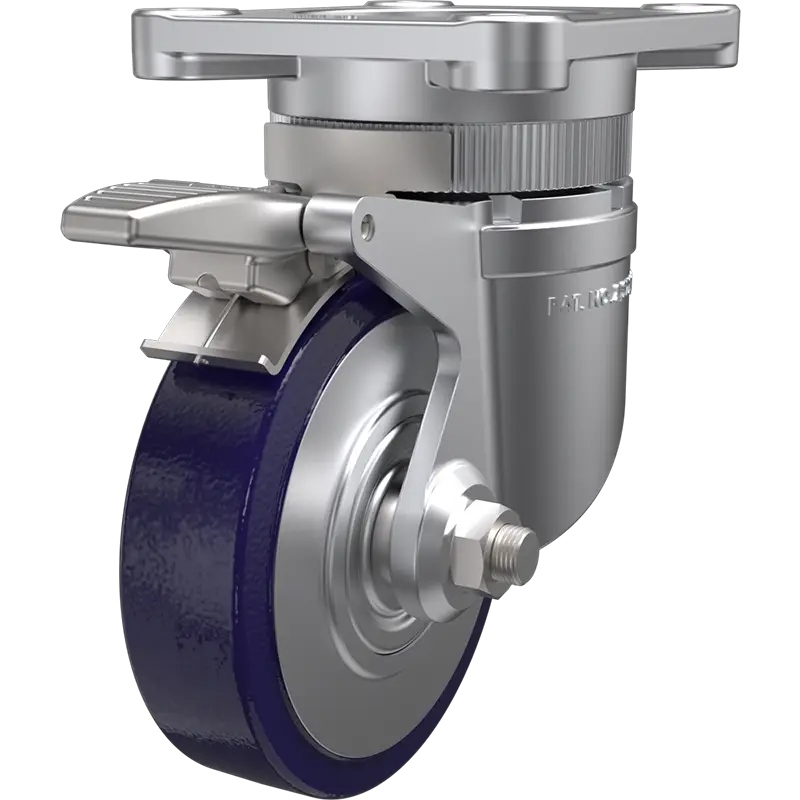
In various industries from manufacturing and medical to retail and warehousing mobility is a key factor in ensuring efficiency, safety, and productivity. Wheels and casters play a central role in making equipment and carts mobile. But there's more to these components than just their ability to roll. As a writer and researcher, I have explored the functional and mechanical differences that define equipment performance. One fundamental distinction that often comes up in industrial design and procurement is between locking wheels and non-locking ones. Understanding this difference can significantly influence both operational efficiency and workplace safety.
What Are Locking Wheels?
heavy duty Locking wheels, as the name implies, have mechanisms that allow users to restrict their movement. This mechanism is typically engaged by a foot pedal or manual lever and can stop the wheel from rotating, swiveling, or both. The primary purpose is to stabilize the equipment to prevent unintended movement.
There are different types of locking mechanisms, such as:
- Wheel Locks: These lock the wheel’s rotation but may still allow the swivel motion.
- Total Locks: These lock both the wheel and the swivel function, providing maximum stability.
- Directional Locks: While not fully immobilizing the wheel, these locks allow it to roll only in a fixed direction, which helps steer carts or machines in straight lines.
In my research, I’ve found locking mechanisms are most valuable in settings where safety, control, and stability are essential such as hospitals, labs, assembly lines, and transport carts in uneven terrains.
What Are Non-Locking Wheels?
Non locking wheels are straightforward in design and function. They allow complete freedom of motion either as fixed-direction casters or as swivel wheels that move in all directions. These wheels are ideal in applications where equipment needs to be constantly repositioned or moved freely without the need to anchor it in place.
Non-locking wheels are commonly found on items like office chairs, display racks, mobile storage units, and shopping carts. In these cases, the lack of a locking mechanism is a feature, not a flaw. It allows for maximum flexibility in usage without the added complexity or cost of a locking system.
Functional Differences That Matter
As someone who closely studies product design and user requirements, I’ve noticed that the choice between locking and non-locking wheels often comes down to the following key differences:
1. Control and Safety
Locking wheels provide a crucial safety measure, especially in environments where equipment should not move unless intentionally relocated. For instance, in healthcare settings, locking mechanisms prevent hospital beds or medical carts from shifting unexpectedly, protecting both staff and patients.
Non-locking wheels, while offering mobility, lack this added control. This can be a risk if the equipment is placed on sloped or uneven floors or in high-traffic areas where accidental movement could cause injury or disruption.
2. Precision in Positioning
Locking mechanisms enable precise positioning of machinery or equipment. When a workbench or machine needs to remain stationary during use, total lock casters are invaluable. Non-locking wheels would fail to provide that level of positional accuracy, which could result in process inefficiencies or even compromised product quality.
3. Cost and Maintenance
Locking wheels tend to be more expensive due to their additional components. They may also require periodic inspection and maintenance to ensure the locking mechanisms are functioning properly. In contrast, non-locking variants are simpler, generally cheaper, and less likely to fail due to mechanical wear.
That said, for critical equipment, the added investment in a locking mechanism often pays off in safety and functionality.
4. Operational Use Cases
During my review of industrial applications, I found that locking wheels are most often used on:
- Medical carts and hospital beds
- Mobile workstations
- Industrial machinery
- Laboratory equipment
- Material handling carts on slopes
Non-locking wheels, on the other hand, dominate environments where constant movement is key:
- Retail store displays
- Light-duty transport carts
- Office furniture
- Service trolleys
Matching the type of wheel to the intended function is essential for performance and user satisfaction.
Application-Specific Considerations
Let’s explore a few specific scenarios to better understand when and why each type might be chosen.
Manufacturing Floor
In this environment, mobile equipment may need to stay fixed during operation but be moved for cleaning or reconfiguration. Locking wheels provide that dual functionality. Machinery with only non-locking wheels could move during use, leading to misalignment or even accidents.
Medical Environment
Medical carts and diagnostic machines are often wheeled around but must be stable when in use. Imagine using sensitive equipment or performing a procedure while the cart moves slightly this could lead to serious consequences. Locking mechanisms are not optional here they are standard safety components.
Retail Display
A retail setting requires flexibility. Store managers frequently rearrange displays to refresh layouts or make room for seasonal promotions. Non-locking wheels make this process smooth and effortless. Locking mechanisms, though available, are rarely used unless the display must remain stationary in high-traffic zones.
Workshops or Garages
In a DIY or industrial workshop, locking wheels on a mobile workbench or tool cart ensure it won’t shift during cutting, drilling, or welding. Non-locking wheels would compromise safety and precision.
Making the Right Choice
When determining whether to use locking or non-locking wheels, it's important to consider:
- Frequency of movement: Will the equipment be moved often or only occasionally?
- Environmental hazards: Are there slopes, vibrations, or potential collisions?
- Precision requirements: Does the task require the equipment to remain perfectly still?
- Load and usage: Will the wheels support heavy loads, or are they for light-duty applications?
It’s also worth noting that some solutions incorporate a combination of both types—two locking and two non-locking wheels—offering a balance between control and flexibility.
Final Thoughts
While wheels might seem like a small component in the grand scheme of industrial or commercial operations, their design and functionality have a substantial impact on safety, productivity, and user experience. The distinction between locking and non locking wheels is more than mechanical it’s a strategic decision that affects workflow, risk, and performance.
In reviewing numerous industry applications and consulting design specifications, I’ve found that choosing the right type of wheel for your environment is crucial. Locking wheels are invaluable in scenarios demanding safety and stability, while non-locking alternatives excel in dynamic, flexible spaces.
Understanding these differences ensures that users and organizations make informed, practical choices that align with their operational needs. As a writer and researcher, I always advocate for decisions grounded in evidence and real-world functionality and when it comes to wheels, that philosophy couldn’t be more appropriate.
- Fashion
- Art
- Causes
- Crafts
- Dance
- Drinks
- Film
- Fitness
- Food
- Oyunlar
- Gardening
- Health
- Home
- Literature
- Music
- Networking
- Other
- Party
- Religion
- Shopping
- Sports
- Theater
- Wellness